Alfa Laval field service engineers secure top performance for rendering decanter centrifuges and separators
Experienced Brisbane-based Alfa Laval field service engineer (FSE) and team lead, Luis Cabeza, shares his advice for maintaining decanter centrifuges and separators in demanding meat processing and animal by-product rendering applications.
DATE 2023-11-27To meet the demand for consistently product quality, separation equipment has evolved over time, into more complex and efficient machines. Luis explains that modern protein decanters and separators require a different services approach and activities.
Alfa Laval decanter centrifuges and separators play a very important role in the rendering process. These machines are exposed to high demanding environment and coarse product. This requires a rigorous maintenance plan that will translate to better separation performance which results in improvement in final product quality.”
Regular, predictive maintenance also avoids unplanned production stops, and minimises the cost of repairs by recording and monitoring machine conditions and wear of main components. Other benefits include a reduction in energy and water consumption.
What happens when an Alfa Laval field service engineer visits a production site?
Depending on the equipment to maintain, Alfa Laval technicians can conduct everything from auditory and condition checks to intermediate and major service onsite. In some case the FSEs can also conduct troubleshooting and optimisation work.
Luis says he normally meets first with the customer’s Maintenance Responsible and machine operators to discuss potential issues or fails. This is followed by a thorough inspection of the machine:
“First I check the machine external conditions, paying particular attention to any unsafe conditions, check the vibration readings, and compare noises, smells, leaks, and product quality.”
One of the most important early warning signs that customers should look out for is the vibration readings. “As mentioned before, feeling the machine gives us a summary of the machine conditions and a possible predictive maintenance. A sudden increase in the vibration level is a sign that something is happening in the machine that will require our attention.”
He adds: “Depending on the conditions observed on the machine that could compromise its safety operation and its performance, we as trained field service engineers are capable of recognising what is the best option moving forward. We will advise the customer if it’s possible to repair the machine on site or if it needs to get fully reconditioned in our service centre.”
What are the benefits of a service agreement?
A service agreement is a win/win Service plan relation for renderers. “One of the most valuable factors is the close relation with customers, knowing their equipment, their process and their machine give us an ample vision how to maintain efficiently their machines.” Alfa Laval can also provide a tailor-made service plan to meet your specific site and operational requirements.
What is the value that Alfa Laval field service technicians can offer to customers?
Many of our customers prefer to buy Alfa Laval equipment not only for the recognised brand of good quality products but also for our strong after sales presence and support, with field service engineers across Australia and New Zealand.
Being part of the Alfa Laval service team gives us the satisfaction of be one key help for the customer needs, knowing that our customers really trust in our advice and recommendations give us more interest and passion in the daily basic activities.
Our customers are really appreciative of the positive impact of service presence in their installations. Our field service team is there to support them, to get their machine repaired and fully operational in the most efficient way, or in many cases just to have their equipment inspected and exchange learnings and best practice.
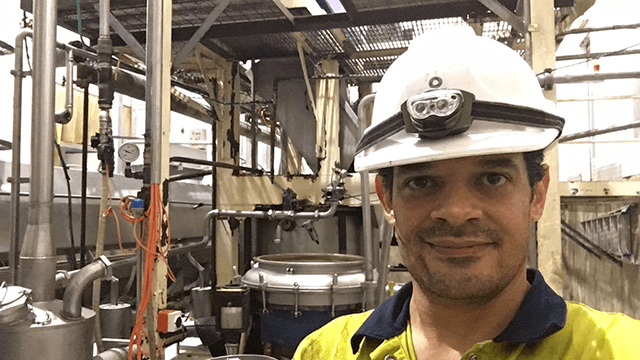
Meet the expert
Luis Cabeza, Field Service Engineer & Team Lead
Based in Brisbane, Luis travels to rendering sites in Queensland and around Australia on a regular basis, working closely with customers on maintaining and optimising their separation equipment in the most efficient way. Being part of the Alfa Laval Australia Service Operations team he enjoys being there for the customer's needs, providing advice and recommendations to make a positive impact and exchanging learnings and best practice with the maintenance team and operators.