Improve productivity and environmental outcomes with sustainable optimization of your fluid handling systems
Looking to cut energy and water costs? Optimizing your process equipment is a sensible and sustainable way to support people, planet and profitability.
If you want to optimize your plant’s performance while boosting profitability, take a look at your Cleaning-in-Place (CIP) systems.
On average, 20% of a plant’s energy use goes towards CIP. Optimizing essential CIP technologies is a proven way to increase sustainability and profitability at your processing plant.
Optimize your CIP processes across the dairy, food, and beverage industries. Get more uptime and significant energy and water savings on while minimizing waste.
More energy-efficient CIP
- Alfa Laval agitators use 80% less energy than conventional agitators
- Alfa Laval pumps cut energy by 30%
More resource-efficient CIP
- Alfa Laval valves with automated burst seat cleaning use up to 90% less water and CIP media
- Alfa Laval tank cleaning systems cut water consumption by 70%
With Sustainable Optimization, Alfa Laval can find ways to help you reach your sustainability goals.
Meet your sustainability and cost-savings targets eBook
The new interactive Alfa Laval eBook, Meet your sustainability and cost-savings targets with Cleaning-in-Place optimization, makes it easy to explore technology innovations and determine cost savings. Real-life customer case stories provide the proof you need to upgrade essential CIP equipment, such as valves, pumps, tank cleaning machines and agitators.
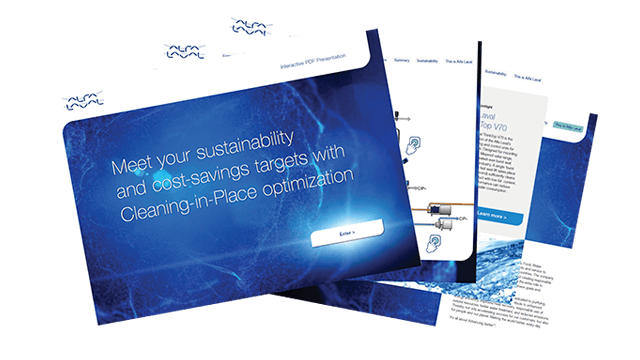
Happy Customers
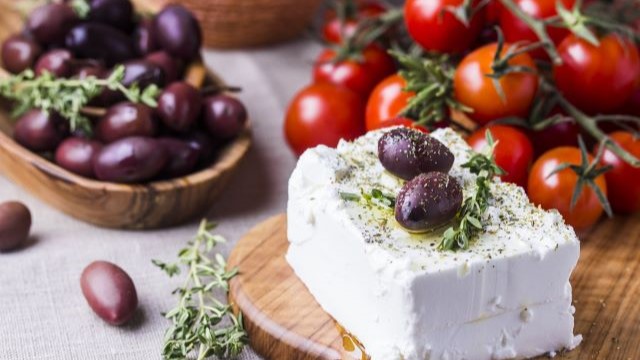
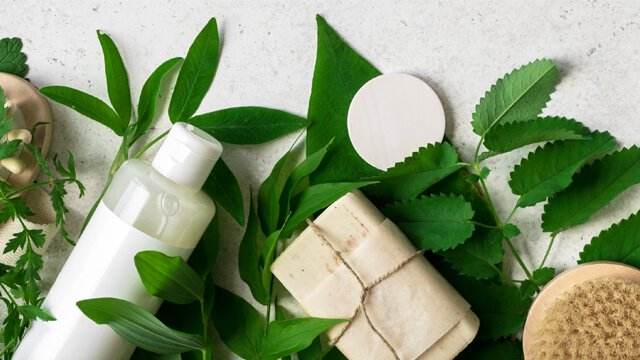
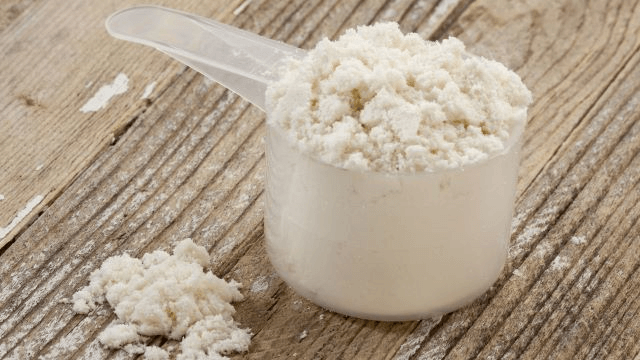
Yörükoğlu Süt, Turkey
"Learning about how Alfa Laval and Tetra Pak could further our sustainability agenda with water and energy savings was eye-opening."
Burak Aksoy, Factory Manager, Yörükoğlu Süt.
Dabur Naturelle, Dubai
"We firmly believe that environmental sustainability serves as the essential element that underpins business success."
Subba Rao, Head of International Operations, Dabur International.
Joint Alfa Laval - Tetra Pak audit
"I wanted to be sure the new pumps would do the job, but the LKH pumps exceeded my expectations."
The dairy’s maintenance manager, Major Dairy Company, Denmark.
Choose the most efficient products for your essential CIP technologies
Alfa Laval LKH Prime Pump
Using the combination of advanced air-screw technology, optimized impeller and casing geometry, Alfa Laval LKH Prime Pump exceeds industry expectations for quiet, efficient operation, reduced energy consumption and CO2 footprint. Alfa Laval LKH Prime is engineered to meet the most stringent standards and hygienic requirements.
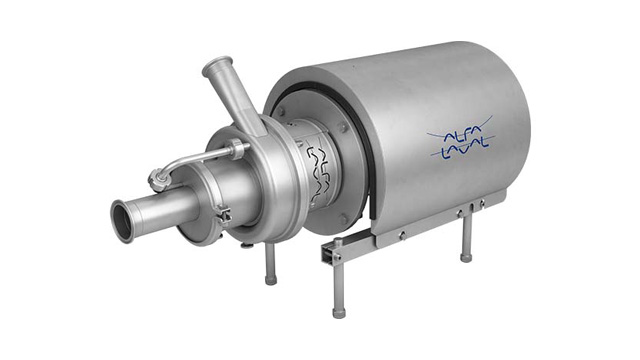
The Alfa Laval ThinkTop® V70
The Alfa Laval ThinkTop® V70 is the next-generation of the Alfa Laval’s leading sensing and control units for hygienic valves. Designed for mounting on our Unique range of Mixproof valves. It delivers the fastest ever burst seat cleaning in the industry, with one ‘burst seat clean’ enough to clean low fat content product from the valve. Its unrivalled performance can reduce water and waste water consumption by up to 90%
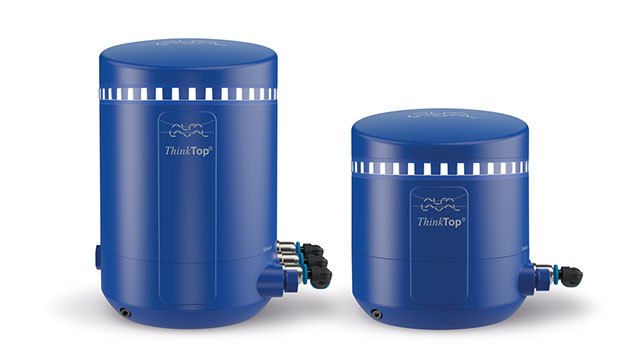
Alfa Laval TJ Rotary Jet Heads
Alfa Laval’s range of Rotary Jet Head tank-cleaning devices provide exceptional cleanability, better end-product quality, greater overall output and up to 70% reduction in operating costs. Avoid contamination with a 360° repeatable cleaning pattern and reduce water and chemicals requirements.
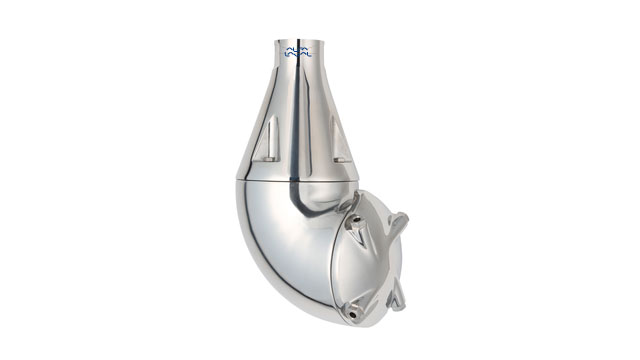
Alfa Laval’s Rotary Jet Mixer
Alfa Laval’s Rotary Jet Mixer does double duty. A single unit can handle liquid mixing, gas dispersion and powder dispersion applications without requiring separate equipment for each process and thereby delivering significant savings. After completion of the mixing process, the mixer’s jet nozzles can be used for spraying cleaning liquids in the tank to effectively clean tank surfaces
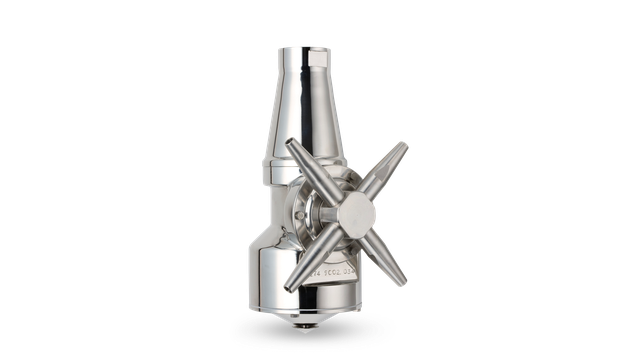
Bring your sustainability strategy to life
Get more energy and water savings and reduce emissions from your hygienic processing lines. Our monthly newsletter, near, brings you stories about how Alfa Laval customers improve environmental performance across the dairy, food, beverage, home-personal care and pharmaceutical industries. What’s good for people and planet is good for your business too.
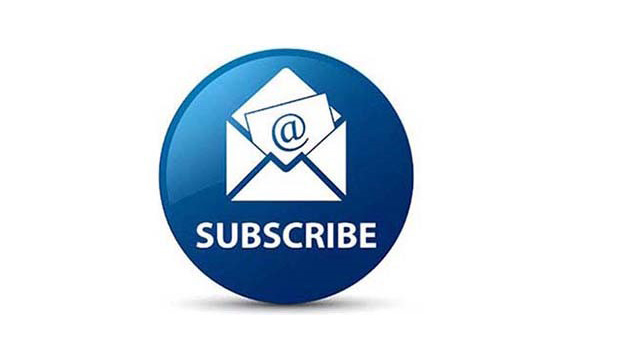